JE Temelín - Store of spent fissionable fuel:
2009 - Novák, Hanuš, BenešSTOCK OF spent nuclear fuel - NUCLEAR POWER PLANT TEMELÍN
INTRODUCTION
Preparation of construction stock of spent nuclear fuel (SSNF) in the nuclear power plant Temelin based on Government Resolution No. 121/1997 from 5.3.1997, which the Government has recommended building storage of spent nuclear fuel in the area of nuclear power plants, as a priority solution to the end of fuel cycle, before placing in the deep repository. Assumed operation of the reactor fuel in a four-year cycle. The warehouse is divided on the two parts – the receiving and the stock part. The building is monolithic reinforced frame structure with precast-monolithic roof.
CONCEPTUAL PROPOSAL and structural analysis
The concept of solution structure is especially designed according to a international standards for nuclear power, which take precedence over the standards ČSN EN and this standarts is a very large complex of rules and regulations. And notwithstanding the fact that nuclear safety and radiation protection is based on security packages files (PF), are structures SSNF conservatively designed for extreme effects of external influences with a low probability of occurrence. This solution enables control and manipulation with PF, even in the emergency of accidental situations. Basic and special combinations of loads are considered accordings rules and standarts IAEA-TECDOC, NS-G and others. The basic combination of the dominant loads considering the following: load cranes, wind, snow, operational utility load and temperature. Extraordinary combination considering separately, seismic loads, aircraft crash, extreme wind, extreme snow, extreme temperature and explosion with constant load. A duktility was carefully aplicated. The construction of foundations was designed in order to, all of the parts of the foundations was uniformly excitatted by seismicity. Increased attention has been paid to reinforcement of critical areas with the mind of plastic joints with a demand for energy dissipation. Decide to the design SSNF were exceptional and extreme load conditions - sesimicity (columns, some of the beams), the aircraft impact (walls), extreme and normal temperature (walls, foundations).
Detailed analysis was devoted to an extraordinary loads - seismicity (return to 10 000 years), plane crash, extreme temperatures and explosion. Temperature stress designs have been verified by detailed numerical models, in considering the gradual implementation of the warehouse. The temperature of the PF reach the temperature to +80 ° C, while the outside temperature is considered in extreme value -46 ° C. Much attention was paid to large volumes of concreting, concrete mix design and the process of concreting. Proposal of the concrete with using blended cements, detailed design process of concreting and reinforcement with consideration of the of volume changes, allow concreting of massive parts heights up to 3.0 m (foundation) and 2.5 m (solid beams, etc.) in one stag, without crak due to volume changes concrete. At the same, concreting large sections accelerate construction. With regard to speeding up the construction, the roof was designed as precast-monolithic..
DESIGN AND CONSTRUCTION
This is an industrial storage facility diveded to two parts - receiving and stock part. Storage part of the layout dimension 46.7 x 74.0 and a height of 24.30 m. Receiving part layout dimension are 25.5 x 67.0 and height of 25.85 m. The foundations is proposed as a two-segment robust concrete foundation strip, which together create a solid base grid. The foundation strip is made in the level of weathered pararul. The lower portion of the foundations strip is 6.5 m x 1.5 m, upper 2.9 x 1.3 m in the stock.. Thickness of a foundation slab made up in the receiving part is 1.2 m with a reinforcing walls of variable width and height of 3.2 m. External walls and supporting columns are fully fixed in foundations. Supporting structure upper buildings are thermally insulated on the outer part and to only to the high of +9.0 meters at the indoor parts.
Bearing system of the object storeThe building stock is divided into three parts. Individual expansion units are dilated in above-ground structures and have common foundations. Storage part of the building is designed as a one-storey building. The bering structure is R.C. frame with the perimeter columns dimension 800/2900mm, 800/3000 mm inner columns and continuous prefab-monolithic truss of the width 400 mm, variable height from 2800 to 3200 mm. Middle columns are integrated into the inner longitudinal wall thickness of 400 mm, perimeter columns are reinforced inner and outer circumferential wall thickness of 600 and 400 mm, which is broken by holes for air. At the level of +9.0 m is a peripheral wall connected to the columns and supporting roof girders at a distance of 6 m and reinforced concrete roof structure. Roof construction is proposed in prefab-monolithic variant and consists of a reinforced prefab concrete girder, which is coupled with the reinforced monolithic concrete slab. Prefab girders acting as T-sections. Prefab girders are not supported on concreting roof slabs. Thickness of roof slab is 400 mm.
Bearing system of the receiving part
The receiving part consists of supporting robust R.C. columns and beams, on which is lay crane runway. Columns are the most powerful dimension of 3600/2700 mm. Basic supporting columns are in the level of crane downloaded a huge reinforced beam dimensions 2000/1900 mm, which also constitute the main girder crane runway receiving hall. Dimensions of columns above the crane girder are 800/800 mm in the axial distance of 5450 mm. Roof construction is prefab-monolithic, similar to the stock parts. Thickness of the walls are 400 mm. Part of the walls is demoutable for the future possibility extend the object of the store.
Applied Materials
The concrete C 30/37 were used for foundations, concrete C35/45 and C40/50 were used for the upper structures of the building. Reinforcement were used B500B and B500C. B500C reinforcement was used in critical regions. Reinforcement of structures was carried out with regard to seismic action, impact of aircraft and explosion. Special attention was paid to critical regions with the potential plastic joints and the necessity of dissipation energy. Foundation construction, columns, walls, roof slabs and girders were largely reinforcing. The main reinforcement is Ø32 mm, walls and roof Ø 28 and Ø25. In most cases, the reinforcement was connected by overlap, uniquely by molded connectors. The shear pins are used to reinforce the roof. Connecting of reinforcement of the periphery columns with prefab girder is done using pressed couplings. Consumption of materials
| Total | Per 1 m3 |
Concrete C35/45 | 22 333 m3 | |
Reinforcing steel | 5 937 t | 265 kg |
Installation of prefabricated trusses
Installation of trusses represented one of the most complicated work on the construction of the SSNF. Transportation unique precast reinforced concrete trusses manufactured in precasting factory PSG, was a difficult and unusual contract for CD Cargo carriers. Isolated beams, each weighing over 100 tons, a length of 23 meters and a height at its highest point about 4 m, had to be shipped to the construction of cars, which enabled the location of truss on two wagons, due to their enormous weight. Fixing was carried out using a specially-made structures. Mounting of the trusses on the columns pins was also very complicaed and their involvement to the structure. Manufacture of trusses and their assembly required accuracy of ± 10 mm.
CONCLUSION
Construction of the SSNF si complicated structure in terms of design, especially the influence of extreme and accidental design situations. Structures for nuclear power are designed according to extensive international standards and regulations for nuclear power, which take precedence over national standards. In the design SSNF was necessary to use results of tests and complicadted numerical analysis.Roofing of the object in precast-molithic variant significantly speed up the construction period and save cost. The proposal of the concrete was made with respect to concreting the massive concrete elements and large volumes in a very short time. Transportation and installation of trusses represented the most complicated part of the construction of the building.
Building construction time was 12 months – it is relatively very short. Quality of design meets the demanding requirements of the project. The option of the monolithic variant with precast-monolithic roof is a competitive alternative to prefabricated options built up abroad. Requierments of the National Nuclear Energy aurotrity is decisive for the choice of the variant of the bearing structure.
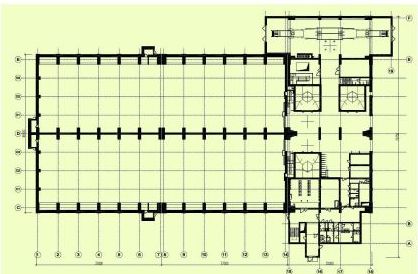
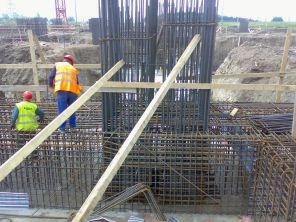